Lock control units
Every Lock electric actuator EWA is equipped with a Lock control unit that can be used to precisely adjust the start and end points, i.e. the end positions of a movement. It is impossible to overrun these end positions, preventing massive damage to the application and even destruction.
Each Lock control unit can optionally be equipped with a position indicator. This measures the distance traveled between the start and end points and reports this to a control system. Precise positioning within the travel distance is possible, as is reaching the start and end points exactly, even over hundreds of cycles.
In order to live up to our claim of offering the right solution for every application and every environment, we differentiate between mechatronic (LSC) and mechanical (END) control units.
Control unit LSC - currentless absolute
Lock has been setting standards since 2019 with the LSC currentless control unit, completely redefining the adjustment of end positions and travel measurement. The control unit offers the option of adjusting the end positions without a power connection. This creates an assembly advantage, as both the assembly and the adjustment of the end positions can be carried out in a single operation.
In addition, this feature ensures that the control unit does not lose the adjustment of the end positions when the drive is moved without power. Instead, the control unit recognizes the exact current position after the power returns. Damage caused by overrunning the end positions is impossible and a reference run is unnecessary. This saves time and money during maintenance or repairs to the drive train.
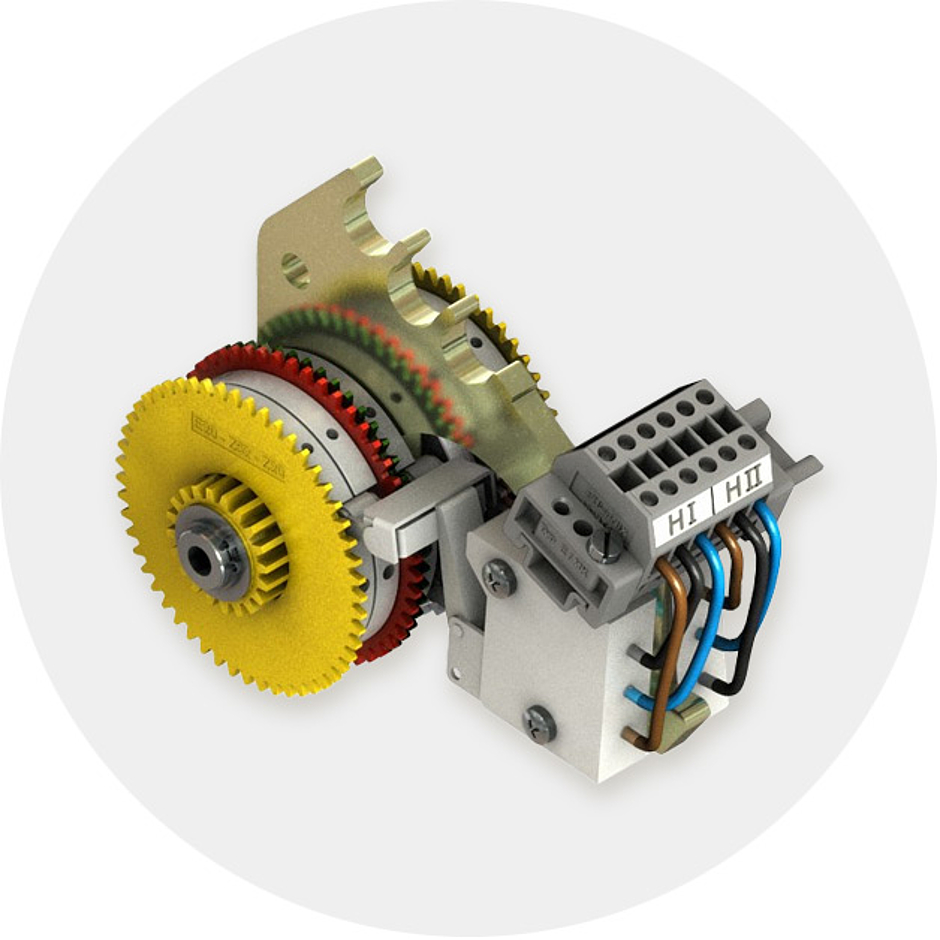
Control unit END
With the END mechanical control unit, the start and end points of a movement, the end positions, can be easily adjusted. Adjustment is carried out by fixing grub screws in the END and is possible without electricity and ensures a simple installation process compared to conventional mechanical solutions on the market.
An optional additional safety switch integrated in the END control unit ensures that the end positions are not overrun even if the position has been changed manually. As soon as the limit switch is outside the range between the start and end positions, the safety switch switches the drive off completely. When the system is restarted after maintenance or repairs to the drive train, no readjustment is necessary with an END including safety switch.
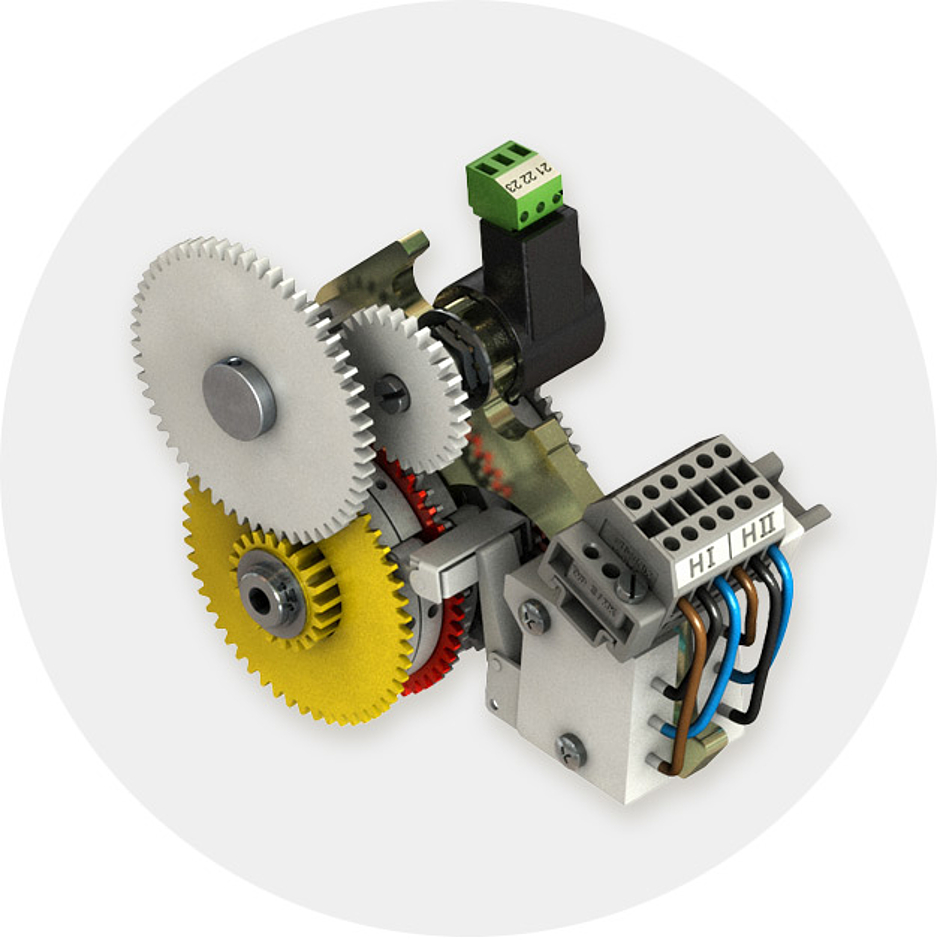
With the PAR position indicator, the END control unit becomes a position indicator. The PAR also adjusts the start and end points of the movement. When connected to a control system, the exact distance traveled and therefore the exact position is reported back.